Large? Check
Heavy? Check.
Expensive? Check
Completely and utterly addicting to the extent that I would start up a commercial spaceflight company, and an electric car company, just so I could allow others to experience the joy of copious amounts of torque and linear power delivery? Check.
We have all heard of
Elon Musk, or at least, we've all heard of his companies
Space X, and more importantly,
Tesla Motors. And because this blog is about me, trying to design, and build an electric autocrosser, I thought that it might be relevant to drive the all new
Tesla Model-S with the P85+ performance package.
Now a little history, not that I think anyone needs it. It's just good writing.
Tesla Motors was founded in 2003 by a number of really smart, really forward thinking, and completely bonkers big wigs. The one that we all know is
Elon Musk. This guy, in my opinion, is the guy who will change the world. Not just because of Tesla, but his whole way of thinking so forwardly for humanity and the world in general. With Space X, he wants to make space travel viable to humans so we can get off this rock and further our presence out in the universe. But for this blog, that is beside the point.
Tesla created a "proof of concept" vehicle with the
Tesla Roadster in 2006 for the prototypes, and 2008 for the "mass" produced versions. It was basically a
Lotus Elise that was customized and fiddled with so that a whole new type of car was developed. A fully electric car that was ridiculously not-boring. It was a brave new step for all gearheads. This was no EV-1. This was an actual, functional, realistic car, that had great range(for electric), and handling to match.
Only 50 made it to Canada, and I have had the pleasure of sitting in 2 of those cockpits. Not easy to get in, but then, that's like saying, planes are not comfortable or smooth while they taxi down the run-way. Of course it's hard to get in. That's not what the car is built for.
After the contract expired with Lotus, and the 2500 Elises that were to be used were converted, it was then time to focus on a real world car that would aim squarely at the BMW-ers, Mercedes-ers and Audi-ers.
That is where the Model-S comes in. With 3 different flavours the Model-S comes in 60kwh, 85kwh, and P85+. The latter is the highest end version, with performance goodies like an equivalent power rating of 416hp/443ft-lb. I've seen dynos that showed much more horsepower than that, but still, 416hp, with all that torque right from 0rpm, well, there is no other word to describe it other than,"WEEEEEEEEEEEHAAAAAAAAA!"
And those words came out of my mouth more than once when I took the test drive. Invited by Tesla to go for a test drive from the
Steamwhistle Brewery in the heart of Toronto (I've done the brewery tour 4 times now and I will do it again. Granted, I'm a bit of a beer nut.) to the
Evergreen Brickworks which is a jaunt on the Gardiner Highway to the DVP artery. I got to experience the Model-S in all sorts of traffic and tight confines of a parking lot full of cars and families going to go skating.
The exterior dimensions are mammoth, The P85+ is almost 5 metres long, and 2 metres wide. And even though it is so large, it doesn't have that sort of in your face bizarre unnaturally forced design like the
Porsche Panamera.
It doesn't look like a car that was originally something else, and in order to make it fill a niche, extended, added 2 more doors, and threw design out the window.
The Model-S is a stunning car. It has a nice low stance. The design flows from the front grill all the way to the rear lights. Granted, it comes with 21" wheels wrapped in Michelin Summer rubber usually, but because we are in the dead of winter, I was on 19" winter tires. It still looked kickin' good, and I even got some, "Nice Tesla" from passer by-ers. I would even choose the 19" rims because they are lighter and with a car with this kind of prowess, less unsprung weight is always better.
I didn't care about the luxuries. I didn't care about the seat warmers, and sound system. I even stopped the representative before she could even start, and stated that I was purely there to test drive the car. She was completely understanding and with that I pushed on the retracted aerodynamic door handles. They gently slid out inviting me to open the door and slide into the driver's seat.
The leather seat was initially very comfortable. I adjusted it electrically so I was as upright and as low to the floor as possible. The seat would soon show it's weaknesses though.
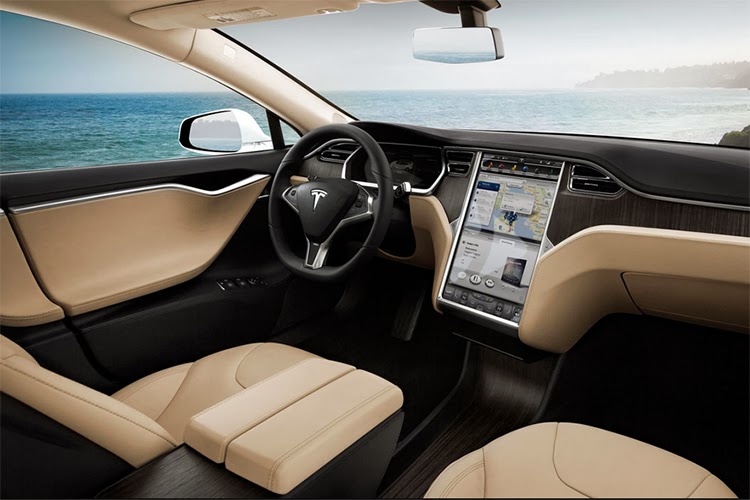
The car is much larger than a car I would be comfortable to drive daily in though, where I live in downtown Toronto. Trying to park in my 1 car garage in my town home complex would be a chore in itself, but, I could still see the relevance to the vehicle, and I truly believe that if any vehicle has to come into downtown, it should be electrically driven. Electric cars are the vehicles for the city.
As I sat into the driver's seat I immediately noticed how spartan the cabin was. It felt very wide and open, and yes, the car is massive so I would think any car this size should feel huge inside, but this is a whole different level of openness. I could put 4 of my dog in the back seats alone, with one on the floor. And he's a 38kg guy!

I could also put another 5 of him in the trunks. I say plural "trunks" because there are 2. One in the front, like a Porsche 911, and one in the rear like any other car. This car is an ocean-going container ship. The amount of cargo space is huge.
I did notice though that the rear window seemed small. The C pillars blocked a lot of my view, and this was evident when I had to do a 4 point turn at the Brickworks to turn around, while making sure I didn't run over any children.
I chose to have the car's regenerative braking pull harder so as soon as I released the go pedal the car would slow, similar to the engine braking in a standard transmission car in a short gear.
I also had the steering weight put into sport so it would be as heavy as possible. I would soon find out that this system is a bit quirky.
The steering wheel, I will say, is almost perfect for me. It is very thick, and has a pleasant tactile feel It's not too large in radius, and it feels sporty enough to me for a touring car. There are no buttons, or consoles that impeded my hands in anyway. I find now a days these convenience buttons get in the way of actually holding onto the steering wheel properly, as if raising and lowering the radio volume is more important than actually gripping the one and only thing that keeps you following the road.
It is fully adjustable and I found the perfect position to enjoy the experience as much as possible. There is nothing worse than an improperly placed steering wheel.
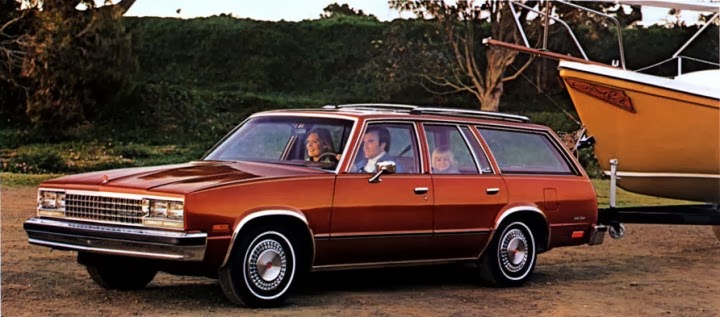
Placing my foot on the brake pedal I shifted the column mounted gear selector into 'D'. It reminded me of my parent's 1979 Chevy Malibu Wagon. Not because the Tesla was anything similar, but that column mounted gear selector really felt old-school, having to make a knuckle-sandwich reversed fist. I would call it almost "nostalgic-design".
A couple of times I went to press in the clutch. A force of habit I'm sure. This was my first automatic in quite some time, and I will say right now, if all automatics were like this car, I would almost consider an automatic transmission in my next car. But since this car has only 1 gear, I can't imagine any automatic being this good.
As we pulled out of Steamwhistle's rear parking lot, and accelerated onto Lakeshow Boulevard, I was given the taste of monumental power in the form of torque. I have never felt such a linear feel in power delivery. With my Sentra, the power is very curvy and once I get into the mid 3000's rpm, that is when the power is noticeable and it ramps up progressively.
With the P85+, as I entered the on ramp to the highway, it was immediate power, and I mean serious, linear power. Even when I was at 100kp/h and wanted to pass someone, the power kicked me back in the seat instantly. I'm glad the Tesla representative that sat with me was pretty cool with me having a bit of fun.
This was where my concern for the car was justified, because as excited as I was to drive this car, I was also a bit hesitant about how it would work. Being that almost everything that normally would be mechanical in a car, the Tesla Model-S was powered by electric motors..
As I was making the curve from the Gardiner Expressway to merge onto the DVP northbound there is a downward ramp that can be done easily at 100kph. As soon as I started to make the bend, the steering unexpectedly pushed back and fought me the entire bend. It didn't feel like a mechanical weight, but more of a dead, electrical motor trying to mimic steering weight. I felt very disconnected from the road then. The feedback was nil. And the artificial weight continued all the way around the bend.
As soon as the curve ended and we were travelling in a straight line again, the steering felt good again. A strange feeling for sure, and one that made me feel uneasy with what I was doing with the car.
Next was the seating. I was noticing in any maneuver, I was sliding around the seat. Maybe the seats are meant for those corporate fat-cats, that are twice my size. Who knows. All I knew was, I really did not like how little lateral support I had, especially with a car that rode so flat and capably around bends.
I could not believe that a car that weighed more than 2100kgs could turn is so nicely. There was a sense of balance, and poise, and as there should be since about 545kgs of batteries are placed at floor level. The COG is the lowest in this class of car.
But those seats, gah!
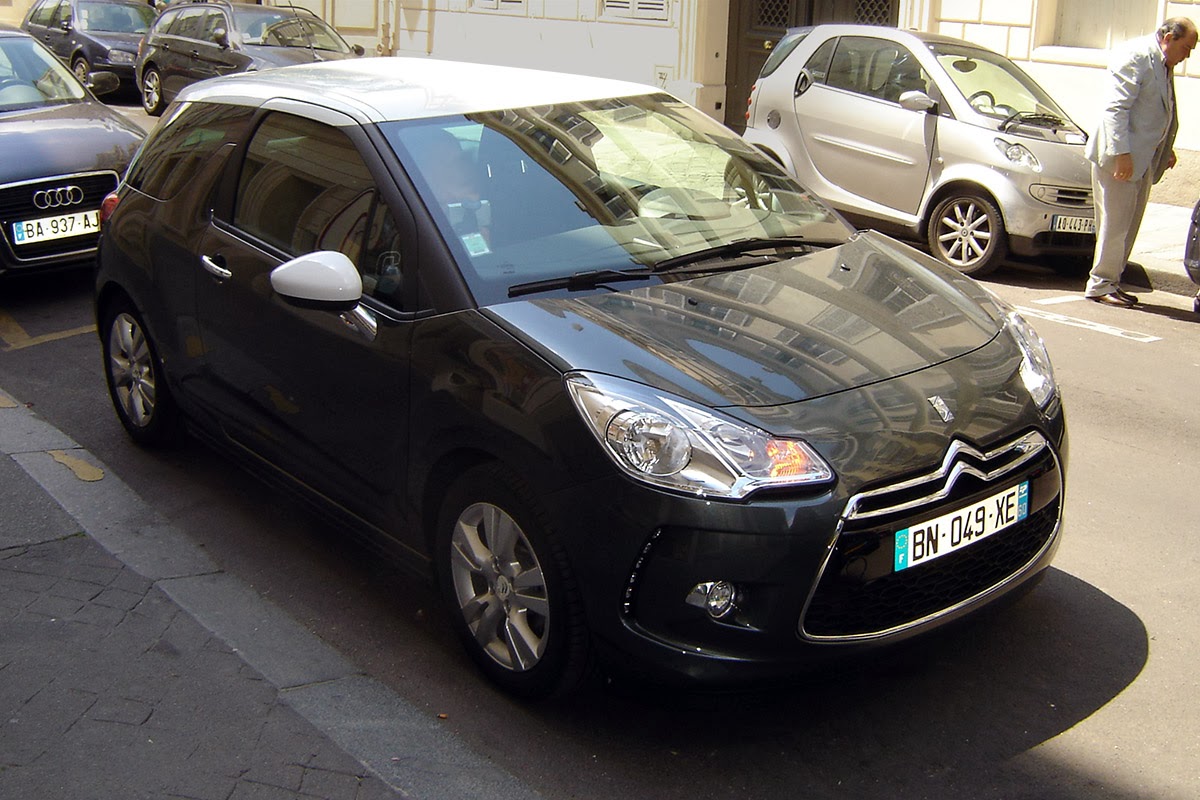
Also, this is completely subjective, and I'm sure that the new technological generation love that 17" LCD centre console. Me, definitely not. I remember back when I drove the Citroen DS3 while I was in France. I loved everything about that car, except the stupid centre console LCD screen. It was constantly shining in my face and at night, made that screen the most distracting, obnoxious gadget ever!
Only, with the P85+ that screen is about 6 times the size. I can only imagine how annoying that thing must be at nighttime. I was told there is a dimmer night mode, but, the DS3 had night mode too. It didn't help. I prefer to be able to see out my front window, and not have a spotlight in my field of view constantly. I think I would maybe try and find someone to hack into the programming and code it so that the screen turned off completely after a minute of not being used, or at least put a sheet of 11" X 17" cardboard in front of it. That should be an option.
I will say though, the screen was crisp, and easy to read. It functioned like any tablet, which made it easy to navigate through.
After about 30 minutes of driving we settled back into the parking lot of Steamwhistle. It was strange how I just slapped the column mounted gear selected into 'R',backed up into the parking spot silently, pressed the "park" button on the gear selector and stepped out of the P85+ without having to turn the engine off, like any standard ICE engined car. All I had to do was exit the car and the car turned off itself. Silently. Waiting for the next person to sit in the cockpit.
The whole experience of driving the Tesla Model-S P85+ was a joy. I hope it would be considering the Model-S with the P85+ package would be more than $125 000 Canadian dollars.
All in all, the car has it's flaws. But then, how often do perfect cars come along. Especially with a company that is barely a decade old, and evolving a technology the is revolutionary.
And, these flaws that I see, are not necessarily flaws at all to the market that the Model-S is geared toward. Executives usually don't care about steering feel. Lateral Support, well, chances are they will never take this car on a track, or do any spirited driving on an open country road. The massive cabin and trunk space would probably sell them on the Model-S. For those things this car is a winner for sure.
The infrastructure for the electric car is still in its infancy but I was told that there should be charging stations continuously from Detroit to Montreal by this year.
The people who ran the event also, were extremely friendly and I had a tonne of conversation with them. They were enthusiastic about their product (which they should be of course) but I could tell that they were genuinely proud of what they offered.
The representative who rode with me has been following Tesla from day one and she applied, and applied, and applied to the company until they hired her. She never gave up, and that is exactly the type of people who Tesla needs to promote their vehicles. Someone who is that passionate about Tesla.
I just can't wait to see in 3 years what the compact version will be like. I'm sure it will be just as big as a winner as the Model-S is. That is, my opinion.